After the workpiece is clamped once in the machining center , the large digital automatic control system can operate the machine tool to select and replace the CNC inserts automatically according to different processes, and automatically change the spindle speed ratio of the lathe, the cutting speed and the relative orbit of the CNC inserts. He assists the worker function, and successively carries out the production and processing of multiple surfaces and multiple processes of the workpiece. And there are a variety of tool changing or tool selection functions, which further improves the productivity.
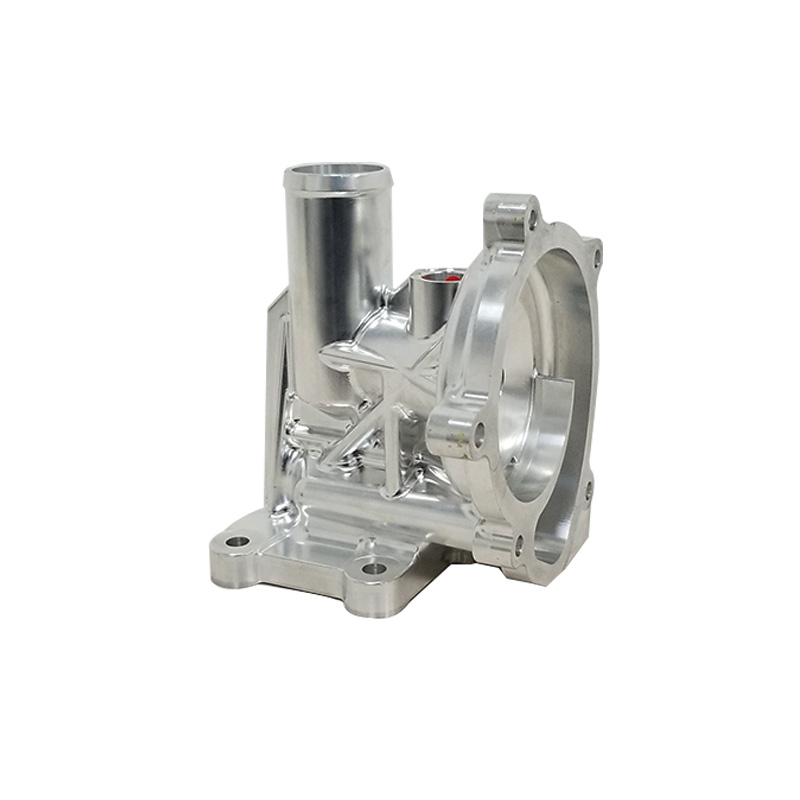
Due to the centralization of the machining center and the fully automatic tool change, the time for workpiece clamping, accurate measurement and machine tool adjustment is reduced, so that the drilling time of the machine tool can reach 80% of the startup time of the machine tool. Only 15 to 20%); in addition, it also reduces the capital turnover, transportation and storage time of the workpiece in the process center, reduces the production cycle time, and has obvious practical effects of economic development. The machining center is suitable for the small and medium-sized mass production of the parts with very complex posture, high precision rules, and frequent product replacement. The machining center is generally called cnc. It is composed of industrial equipment and numerical control machine tools and is applied to the production and processing of complex posture workpieces. High-efficiency automation technology machine tool. Machining center is also called computer gong.
The machining center is equipped with CNC knives, and it is a CNC lathe that performs multi-process production and processing after one-time clamping of the workpiece. The machining center is a high-width ratio mechatronic product. After the workpiece is clamped, the CNC machine tool can operate the machine tool to automatically select according to different procedures, replace the CNC blade automatically, and automatically change the spindle bearing speed ratio, cutting speed, etc. Continue to carry out several processes such as drilling, boring, milling, reaming, tapping, etc., thus greatly reducing the workpiece clamping time, accurate measurement and machine tool adjustment and other auxiliary tool process time, the production and processing posture is very complicated, and the precision rules are relatively high. high.
on the machining centerThe characteristics of the machined parts are: after the machined parts have been clamped once, the CNC machine tool can operate the machine tool to automatically select and replace the CNC blades according to different procedures; fully automatically change the lathe spindle speed ratio, cutting speed and CNC blade relativity. The track of the workpiece and its function keys continue to fully automatically carry out multi-process production and processing of turning holes, countersinking, reaming, boring, tapping external threads, and cutting for each production and processing surface of the workpiece.
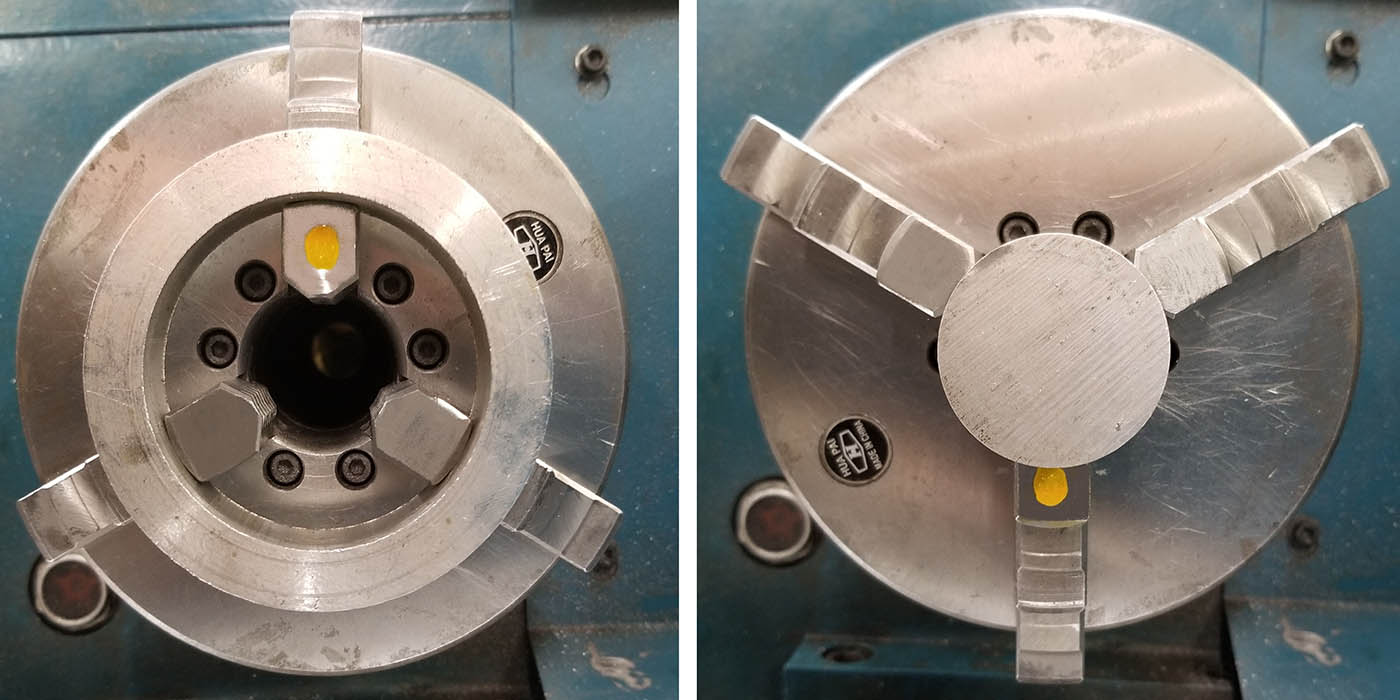
Because the machining center can gather and actively carry out a variety of processes, it can prevent the actual operation deviation of human factors, reduce the workpiece clamping, accurate measurement and the adjustment time of the machine tool and the workpiece capital turnover, transportation and storage time, It further improves the high efficiency of production and processing and the precision of production and processing, so it has excellent economic benefits. The machining center can be divided into CNC machining center and gantry machining center according to the position of the spindle bearing in the indoor space .