ENGINE REBUILD SOLUTIONS APRIL 2022
Check out these Shop Solutions from builders across the country!
CLEAN CUT
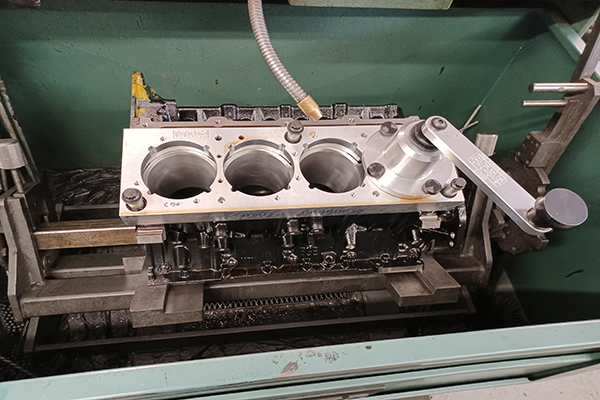
When cutting O-ring and receiver grooves for top fuel hoops, it’s important to have plenty of cutting oil to get a nice clean cut in the heads and block. Instead of spraying penetrating oil all over the bench, we do them in the honing tank and flood the work with oil while cutting. It seems to cut much easier and cleaner without the mess. We use filter screens in the tank as well as a large Sunnen filter cabinet to help keep the oil clean.
Jake Sampson, Sampson Racing Engines, Inver Grove Heights, MN
HOW FITTING
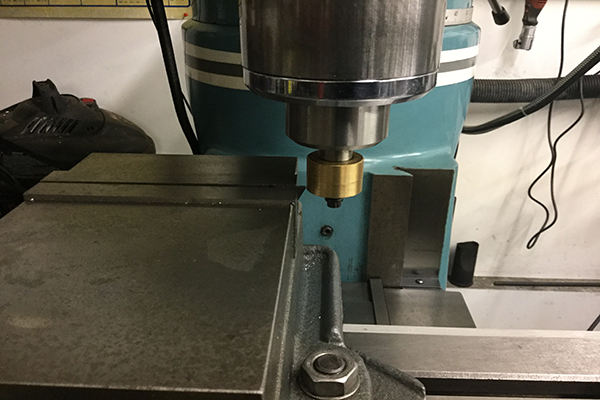
On some crankshafts, the pilot bushing bore is undersize or irregular. Driving in a bushing with too much interference would lead to the I.D. of the pilot bushing being too small for the transmission input shaft. Simply mic the bore and adjust the bearing you are replacing it with by turning the OD. If there are steps in the crank bore, make that adjustment as well. .003” press fit is good.I prefer to use a spud in the mill collet, turning against a fixed bit. I do this for valve guides and many operations just using a collet and the part.
Ron Flood, Cedar Machine, North Branch, MN
REMOVING PIPS
Often when parting off a work piece in the lathe, the tool may leave a “pip” or thin ring attached to the work piece….even when using a right-hand cut-out insert or blade tip. Here’s an easy, quick way to remove the unwanted “pip” or thin material: open a mill vise,with the standard steel jaws, just wide enough to allow the work piece to slip between the jaws. Use a mallet to gently tap the work piece into the space between the jaws, shearing off the pip/ring, for a smooth finish. There are no unsightly scratches from filing, snips, or sanding belt, etc. Example: Removing thin ring of material left behind after parting off custom machined mount for aero engine application.
Tom Nichols, Automotive Machine & Supply, Inc, Cleburne, TX
BEFORE COVID AND BEYOND
Way before the Covid virus I was concerned with getting infection by customary handshaking. I was cutting or scraping my hands on a regular basis in the shop. To keep any germs from entering my body I used the “newskin” liquid bandage to seal them out. Even though handshaking is not what it used to be I still damage my hands now and then and I use the New Skin liquid bandage to seal out germs.
Lyle Haley, The Shop Doc, Andover, MN
In the past, I balanced individual parts like everyone else; match all to the lightest, piston to piston, rod to rod, etc. But a few years ago, I started following this procedure: Assign all parts an identifying letter, then weigh and record all weights. Then match up heaviest piston with lightest rod small end, 2nd heaviest piston with 2nd lightest rod small end,etc. Then once all pistons are matched with all rods, the weight that needs to be removed will be markedly less. Then match heaviest rod big end with lightest rod big end, etc, until all rods are paired up. I made an excel spreadsheet that does the arithmetic, so I don’t get confused. Doing this has cut my component balancing time in half, maybe more.
Mark Workman, Workmonster Motorsports, Ballwin, MO
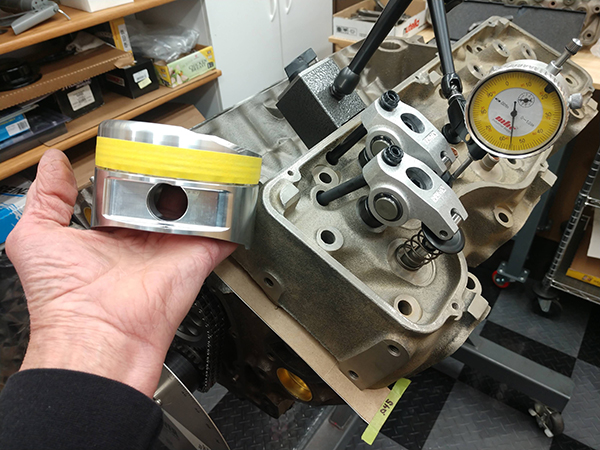
When I mockup to check for piston to valve clearance or pushrod length, I use cardboard strips to simulate the compressed gasket thickness. I lightly snug down a couple of bolts and save the gaskets for the final assembly. Another handy mockup tip is to wrap masking tape around the ring land area of your piston. Just enough to get the “rock” out and tighten its fit in the bore. No wear and tear on the rings and less chance of breaking or chipping one. I never put in the pin locks during the checking in case adjustments to the valve pockets are needed.
Randy Torvinen, Torvinen’s Machine, Menahga, MN
In this article:Shop Solutions