In the context of high-horsepower engine building, the pressure on a cylinder head can be so great that it can, in effect, marginally push it away from the engine block. This makes engine sealing one of the more prevalent challenges, and it gives whole new meaning to the phrase “keep your head down.”
There’s nothing inconspicuous about a blown head gasket, so to prevent it, we dug into the ever-changing technology of head gasket sealing and learned first-off what’s good for high-horsepower isn’t necessarily good for all. Theoretically, on all levels, head gasket sealing simply comes down to surface pressure. Maintaining sufficient surface pressure between the gasket, the head and the block is what prevents leaks.
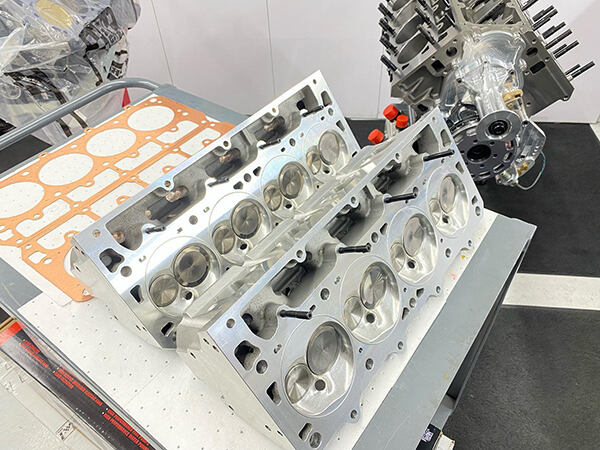
The gasket is only one of many interrelated factors involved, but it is nonetheless a critical component, and therefore a critical decision. Understanding the different types of head gaskets and their pros and cons is the best way to know what to use at what level, but it also comes down to knowing the different products from different manufacturers that can determine exactly which gasket is best for any given build.
Reaching levels well over 1,000 horsepower is not uncommon by any means for today’s engine builders, so the “pressure” has definitely been put on gasket manufacturers, but before we get to that, let’s look at where we’ve been to put a perspective on it all.
A traditional composite was historically the most common style of head gasket, with regular use on production vehicles up through the ‘70s. They were able to handle the compression ratios of the muscle cars of the era, and they did a great job of sealing oil and coolant, since they were very forgiving. This was an important quality, especially in the realm of mass engine production that often suffered in quality, such as surface preparation or manufacturing tolerances.
The desirable aspects of a composite gasket make it perfectly acceptable for standard engine service on vehicles originally so equipped, but as the popularity of the supercharger and turbocharger grew, along with the quest for higher horsepower, the weakness of the composite gasket was easily exposed. Bill Atkinson of Elring explains, “Composite gaskets are compatible with rougher surface finishes and are the least expensive, but they have the shortest service life, and weakest combustion seal.”
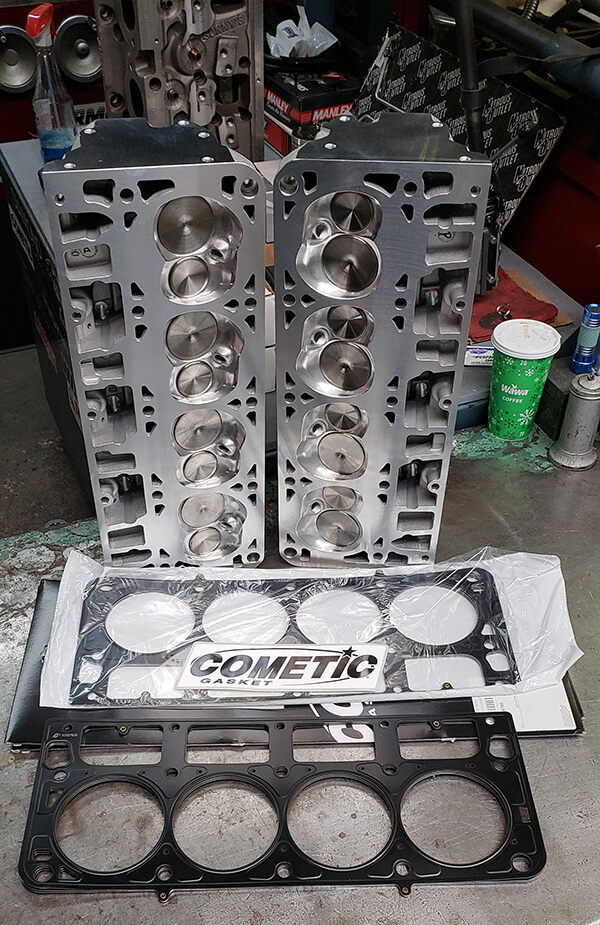
The weak points of a composite gasket saw it abandoned by engine builders and vehicle manufacturers in favor of the MLS (multi-layer steel) head gasket. An MLS gasket has an immediate advantage in its ability to maintain clamp-load, even under the stress of high compression. The general concept of an MLS gasket is layers of carbon or spring steel, with embossments that create a spring pressure in order to maintain the clamp load.
MLS head gasket technology focuses on the design of each individual embossment, depending on its location, to create the necessary clamp loads for compression, coolant and oil sealing. Most MLS head gaskets also have a coating over the entire gasket, and some have additional beads around specific oil and coolant passages. Current research focuses on the location and thickness of the coatings for precision control of clamp load in different areas.
The MLS gasket itself was a considerable improvement in technology, but it is not the gasket alone that has made it successful. “MLS gaskets offer an extended service life and a good to excellent combustion chamber seal,” says Atkinson, “but their sealing performance is dependent on surface finish.”
MLS head gaskets, while superior, are not as forgiving as a composite gasket, and the need for a higher precision of engine machining is a necessary part of MLS head gasket sealing. “Nowadays, because newer technology, machining and parts capabilities have been greatly improved, almost every car manufactured today uses MLS technology,” says Micky Hale of Cometic Gasket.
MLS head gaskets are far more than the first choice of auto manufacturers. They are well suited for many high-horsepower builds. “In today’s high-performance world, a 1,500-hp engine is almost an everyday occurrence,” Hale says. “All of the Cometic MLS or MLX head gaskets being stainless will handle this horsepower and usually a bit more. We do have customers with twin turbo LS-powered vehicles reporting in the 2,000-plus hp range as well, so the package of parts along with modern technology has really come a long way.”
MLS head gaskets have proven their ability to handle high horsepower, but there are still different designs within the MLS line, and additional types of head gaskets that are designed for horsepower levels topping the 1,500 mark. “A standard MLS Spartan and our Copper ICS will seal high 800/900-1,200/1,300 hp depending on the engine architecture,” says Mike Couture and Aaron Hunter of Athena/SCE Gaskets. “Our MLS Spartan with Gas Stopper will seal up to 1,500-1,700 hp, and our Vulcan Cut-Rings have sealed 2,300 hp on an LSX setup and 2,000 on a Coyote. The traditional Pro Copper head gasket with a stainless-steel o-ring and receiver groove will seal until the head flexes or stud threads are pulled, or pistons/rods break or cranks are sent back into the earth.”
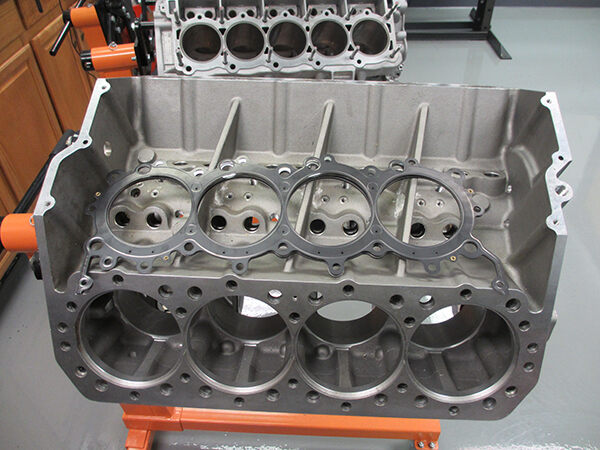
Just as an MLS gasket relies on precision machining for sealing, all gaskets rely on several factors including block and head rigidity, open or closed deck, number of bolts or studs per cylinder, the bolt or stud proximity to the cylinder wall, how deep the bolt or stud is in the block casting and bolt or stud size.
It’s no secret that fastener quality is critical in any aspect of engine building, so cylinder head fasteners, which are subject to different stresses, should always be considered as part of engine design. “The fastener material used must be correct for the application,” says Hale. “While a standard off-the-shelf stud may be great to begin with, installing a power adder with big boost may need a higher-quality material option. It is always best to plan and use the correct package of parts or overbuild to start with. For most of us hot rodders, more power is always on the back burner.”
Cylinder head fasteners play an equal role in maintaining clamp load, and while a gasket manufacturer does all the research and engineering to provide the gasket, an engine builder shoulders the responsibility of not only using the proper fasteners, but ensuring the proper method of installation. “When we see engine builders reusing fastener hardware, consideration should be given to the white paper ARP released about micro-galling on the thread faces and therefore friction, which advances the torque reading on a torque wrench but doesn’t actually achieve proper clamp load,” says Couture and Hunter. “Fastener quality is a major concern. Whenever we have a customer call in and say the gasket failed, our question is what caused the gasket to fail? Did the assembly prep fail, the assembly procedures fail, the components used to clamp the gasket fail, the product selection for the application fail, or were the components pushed well beyond their designed parameters?”
On the subject of installation, a common question is sealers. Should you use a sealer on a cylinder head gasket? I always thought the answer was no.
“The Cometic MLS and MLX already have a proprietary sealer on them, we do not recommend the use of any other additional sealers,” Hale says. “If everything is prepped and compressed properly, they should not leak. Ninety-eight percent of the time when someone calls in about a leaking MLS gasket, this is usually the case. Putting a copper coat on the gasket is like adding a layer of liquid to it and you are not letting the embossments do the sealing they are supposed to do.”
While the answer is often no, that’s not always the case and it’s imperative to follow all instructions or recommendations for the gasket you are using, because there could be different requirements.
“All of our copper gaskets are recommended to be sprayed with a light coat (emphasis on light coat) of KW brand Copper Coat on both sides of the gasket,” SCE says. “Even on our Titan and ICS (with silicone bead seal) we recommend this. Our MLS Spartan has a proprietary coating that is designed to go on dry, use of any additional sealants will compromise the gasket’s ability so seal the combustion. The Vulcan Cut-Ring is to be installed dry without any additional sealants. I always remind people of the 8th grade science class experiment where you have two plates of glass and a drop of water. Press the glass plates together and the water goes out to the edges of the glass. Well, what happens if you do that same experiment with a drop of viscous silicone? Yes, the studs/bolts will squish the excess out, but that’s clamp load used on moving the silicone instead of the combustion seal. Also, where does all that extra silicone go when it does get squeezed out?”
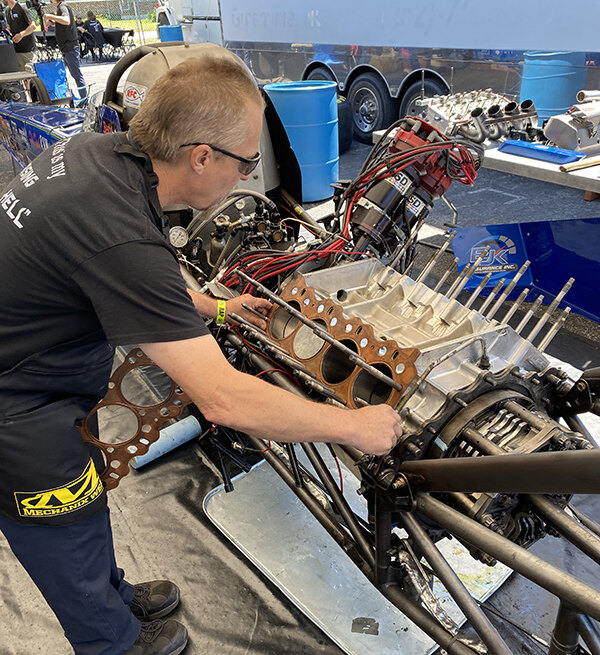
If you’re looking to go off the charts with horsepower, you might be considering a dry deck, and there’s multiple gasket options here as well. One of the biggest differences compared to coolant is the design and location of the embossing. Gaskets designed for no-water applications eliminate the water passages on the gasket, but it’s not entirely necessary. “Contrary to popular belief, even if a customer is running a dry deck, they do not need to run a no water gasket,” says SCE. “A gasket with coolant provisions will seal up just as well.”
Copper head gaskets offer many advantages for extreme applications and a groove machined into the block or head to accept an o-ring is the most common practice with this type of gasket. By installing an o-ring, the clamp load is increased in the area of the combustion chamber, when without it would be distributed evenly across the gasket, and not provide an adequate combustion seal. Another advantage of copper is its ability to conduct heat. This provides more even block and head temperatures, and combustion chamber hot spots dissipate quickly.
Copper head gaskets also provide a certain amount of elasticity that is not present in other head gasket materials. On nitrous, turbocharged or blown engines that truly have the ability to lift a head off the block, this aspect of copper makes it the only one that can handle such abuse.
Among the many things to consider about your engine build when selecting the proper gaskets are two other notable elements – boost pressures and cubic inches. According to SCE, an MLS gasket should have no issues holding under 20-35 psi of boost, but more than that warrants a copper gasket.
“Boost is the biggest determining factor,” SCE says. “Combustion pressures and tuning are a large reason why gaskets will fail. Cubic inch plays a big role too. It goes hand-in-hand with boost. Are you using a big block Chevy that has large cubic inch and a little bit of boost to get to 1,500 hp, or are you using a small, 4-cylinder with 4 bolts per cylinder and boosting it to the moon in order to get there? Cubic inch along with combustion pressures all play a determining role in the equation.”
Depending on your unique engine setup and what you plan to use in terms of boost, cubic inches, cooling, tuning, and horsepower all factor into whether MLS or copper gaskets are a better choice. Going on horsepower alone, MLS gaskets are more than capable at 1,500-hp.
Engine sealing may not be an exact science, but it’s awfully close. If you take advice from the pros and follow their specific instructions, you should have no problem keeping your head down at the races.