As many of you know, under higher combustion pressure, having your cylinder head(s) effectively clamp down the block surface is absolutely critical. Therefore, choosing a brand of head stud that you trust to get the job done is just as important.
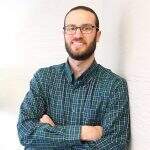
Whether you have a work truck that gets beat to hell all day, a truck built for all-out performance, or something in between, there’s no doubt all truck applications would benefit from a new set of aftermarket cylinder head studs.
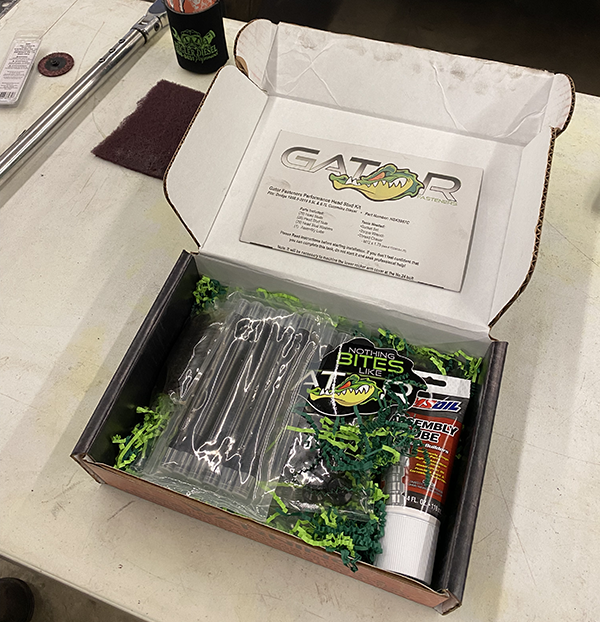
As many of you know, under higher combustion pressure, having your cylinder head(s) effectively clamp down the block surface is absolutely critical. Therefore, choosing a brand of head stud that you trust to get the job done is just as important. Recently, we spoke with ARP about its head stud offerings, and we also spoke with Zeigler Diesel Performance, a diesel shop in Canton, OH, about Gator Fasteners, to get the latest on each company’s head stud specs and tech, as well as some of the similarities and differences as it pertains to the diesel crowd.
Why Upgrade?
Generally, these days, factory fasteners are a torque-to-yield, one-time-use fastener. That means, the likeliness of you lifting the cylinder head off the block and compromising the head gasket is pretty high, over time. Aftermarket studs such as those from ARP or Gator Fasteners will not stretch like factory head bolts since they’re not torque-to-yield.
“For diesel performance, we generally made something that was 20% stronger than the factory hardware,” says Chris Raschke of ARP. “That was the focus and goal. We also wanted something that was reusable. A lot of folks we talk to utilize the ARP2000 and the 625 head studs.”
ARP offers head stud kits for a multitude of different gas and diesel applications, and Gator Fasteners cover the major diesel engine platforms as well. However, Gator doesn’t seem to be as involved on the gas side of the market, but does carry an LS head stud option.
For diesel engines, Gator has studs that fit the 2001 Duramax engines all the way to the newer L5P engines in 2020. Powerstroke and Cummins engines are both covered from ‘89 Rams to the ‘94 Powerstrokes all the way to the current year.

Gator Fasteners have a tensile strength of over 220,000-psi and will not stretch like factory head bolts. They come manufactured with rolled threads after heat treating that provides optimum fatigue strength. They are centerless ground to assure concentricity, and each kit includes heat-treated, chromoly steel, 12-point nuts, and parallel-ground washers with a black oxide finish for extra durability.
While Gator may provide a quality product, naturally, as a new brand, it still lacks what is one of ARP’s best and biggest differentiators – experience.
“We utilize torque tensioning machines to test the factory fasteners and use the factory installation method to test how much clamp load you’re getting from the factory fastener,” Raschke explains. “That’s what we build around from there. We also have a hot test fixture, which is basically an oven with the test unit inside of it, and you can actually heat all the components to operating engine temperatures so you can see the effects of it on the fastener at operating temperature. Those are all the things we take into play when we build a fastener kit for any application. We have a lot of tools in our tool chest to do what we need to do.”
Fastener Material
In the old days, fasteners used 8740 material at 180,000-200,000 psi, which was always more than adequate to replace the factory hardware. Today, a brand like ARP offers customers ARP2000, Inconel or Custom Age 625 PLUS options that have higher tensile strength.
“With 8740 material, you can only take it up to about 200,000 psi, which is right around 38-42 Rockwell, and that’s where its happy,” Raschke says. “If you try to take it higher than that, you’re going to fatigue the head stud. You have to choose materials that will perform where they’re supposed to perform.”
The ARP 2000 performs really well at 220,000 psi and, according to Raschke, it has the properties to still fatigue well and it’ll give good ductility at that higher clamp load. From there, ARP suggests its Custom Age material.
“One of the great features about Custom Age is it’s a stainless material and doesn’t rust,” Raschke says. “It has a high tensile strength (260,000+ psi), so you could crank it up and it’s happy still. It’s also stainless, and the thing about diesel engines is they have a lot of heat, moisture, exhaust gases – everything that is wrong for a regular, generic, steel piece of hardware. Corrosion will create hydrogen and hydrogen embrittlement will break the fastener. If you over-heat treat a stud to make it stronger, you double your chances of having that issue with the hydrogen embrittlement from corrosion.”
Of course, not only does the material make a difference in the head stud that best suits your needs, but so does its size. By in large, most Cummins applications will be just fine utilizing a 12mm head stud. But, some of the real high-performance folks might utilize a 14mm stud, a 9/16ths stud, or even a 5/8ths stud.
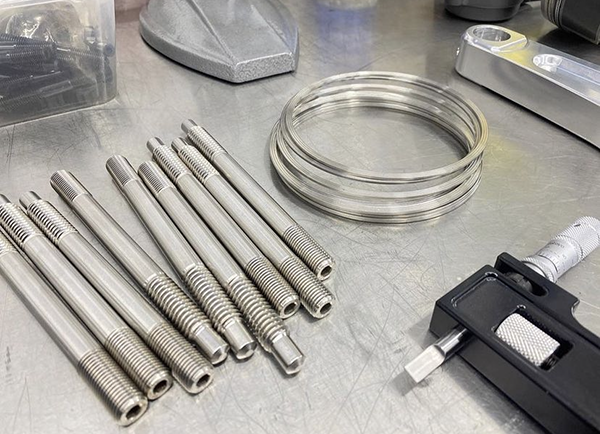
“For the most part, all your Cummins factory stuff is all going to be 12mm for head studs,” Zeigler says. “In the race world, we have been using a 14mm or 9/16ths to have a stronger torque yield. The head studs in my race truck are torqued to 250 ft.-lbs. These 12mm are torqued at 125 ft.-lbs. There’s a significant holding difference, but it’s also a very, very different application.”
Raschke says a lot of Cummins guys started drilling the blocks for larger studs simply because they used to not have a strong enough stud material. Now, thanks to ARP, they do.
“While people still want to machine the block, we offer them a stronger material to a certain point,” he says. “Our solution generally is to make a better-quality fastener that’ll bolt into a factory application. If you want to do something that’s modified, our specialist department is crazy. We do that all the time for a lot of the different diesel guys such as Scheid, Haisley, Wagler, and others.”
While bigger sometimes sounds better, Raschke warns against it depending on your block, heads and what needs to be done in order to utilize that larger stud.
“With these billet blocks, some guys use 9/16ths or 5/8ths even,” he says. “Eventually, you could put in the biggest stud you can, but the cylinder wall isn’t going to hold it or the area for the head gasket isn’t there and you’re going to collapse the block. Maybe the column on the head is not stout enough to support higher clamp load? There’s a lot of things to take into consideration as opposed to just putting something stronger in there. You’ve got to have head gaskets designed property to handle it too.
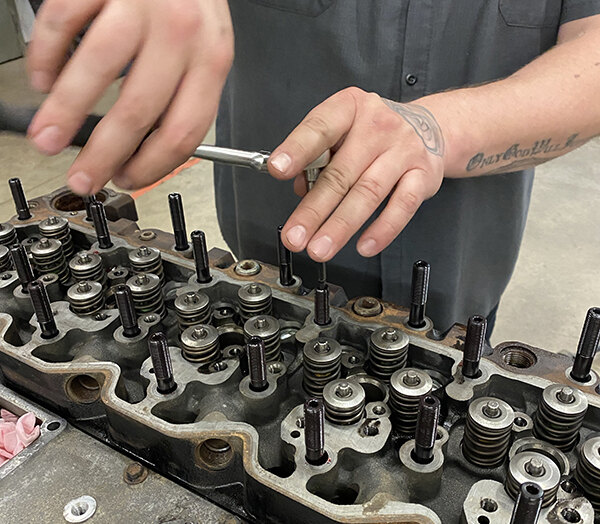
“With the multi-layered gaskets they sell today, you need to have a fastener that’s more forgiving on a street vehicle than it needs to be on a race vehicle, because with a race vehicle you’re probably going to be taking it apart and servicing it more often, whereas the street vehicle needs to last a couple hundred thousand miles. You can’t crush the head gasket down and not have it be able to expand and contract.”
Zeigler echoes those comments by saying most applications don’t require the larger sized studs or super strong material.
“If it’s a mild, nothing absurd application, there’s no reason for that expense,” Zeigler says. “A quality set of head studs with a good head gasket and quality prep work should have no issues if the job is done correctly.”
Installing Studs
As is the case with most engine work, doing the job correctly is 99% of it. The same applies for head stud installation. We met up with Justin at Zeigler Diesel Performance to see the installation of Gator Fastener’s 12mm head stud set for a 24-valve Cummins.
Right off the bat, Justin was complimentary of Gator’s packaging and presentation. Both Gator and ARP studs come in a similar-sized box that includes the necessary hardware, a brand sticker and install instructions. ARP studs are typically encased in individual plastic sleeves and the nuts and washers come in plastic baggies. With Gator Fasteners, the studs were in a nice, plastic case and each stud had plastic end caps to protect the threads, while the washers and nuts were in separate bags. One of the bigger differences was in the lubricant provided. ARP provides a small packet of lubricant, while Gator provides a large tube of AMSOIL assembly lube.
Before any studs get put in place and after you’ve run a tap in each hole, cleanliness is critical to ensuring nothing goes wrong later on.
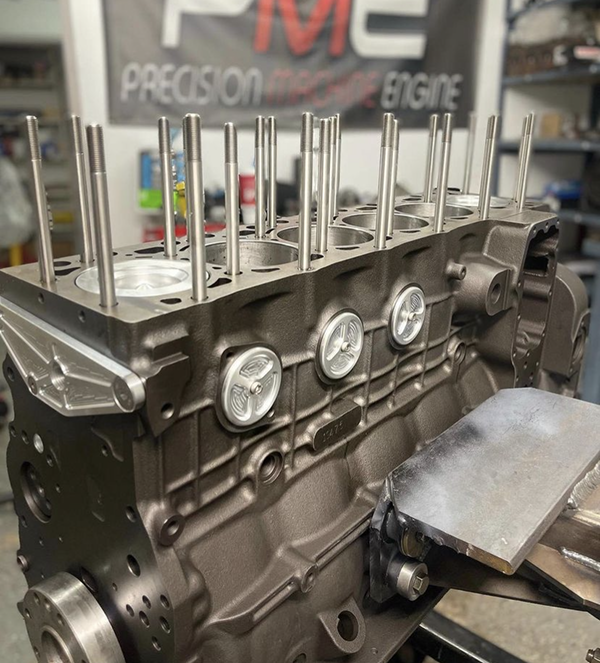
“The biggest thing is the attention to cleanliness,” Zeigler says. “When you’re done tapping the holes, you have to blow them out with air and wipe everything down with brake cleaner to make sure we have everything very, very clean before we put the gasket on the surface.”
The Gator stud kit for the Cummins came with 26 head studs – six longer studs for the outside of the head and 20 shorter studs for the inside. Each stud gets an application of assembly lube before being placed into the head and block. Similar to the ARP2000 studs, these 12mm Gator’s required three torque sequences to get to 125 ft.-lbs. (40, 80 and 125). ARP’s 625 studs on the other hand, go to 150 ft.-lbs. (50, 100, 150). Directions for both brands very easily outline how to go about torquing the studs into place.
As mentioned, ARP designs all of its fasteners so its recommended installation is only at 80% of the load, giving you a 20% cushion if you want it tighter for expansion. What neither Gator or ARP tell you is whether their studs can be reused. Justin can tell you from first-hand experience that you can.
“My sled pull truck years ago had the same ARP studs in it for five different engines,” he says. “I measured them and nothing had stretched and nothing had changed, so I kept using them and never had an issue.”
Depending on the job, a stud install could take 4-6 hours. The only thing you cannot equate for, unless you have a machine shop in-house, is sending the head(s) out to get decked.
Common Mistakes
All in all, head studs aren’t rocket science and neither is the installation, but you still want to ensure you do the job right because the repercussions of doing it wrong can be catastrophic.
“The main key is to pick a proven combination,” Raschke suggests. “Guys go online and pick this turbo and that injector and this head gasket and that fire ring, and they mix all this stuff together and something doesn’t work out. They use ideas from four or five different people as opposed to picking a combination that’s suited to their needs. You need to always look at the big picture when building something.
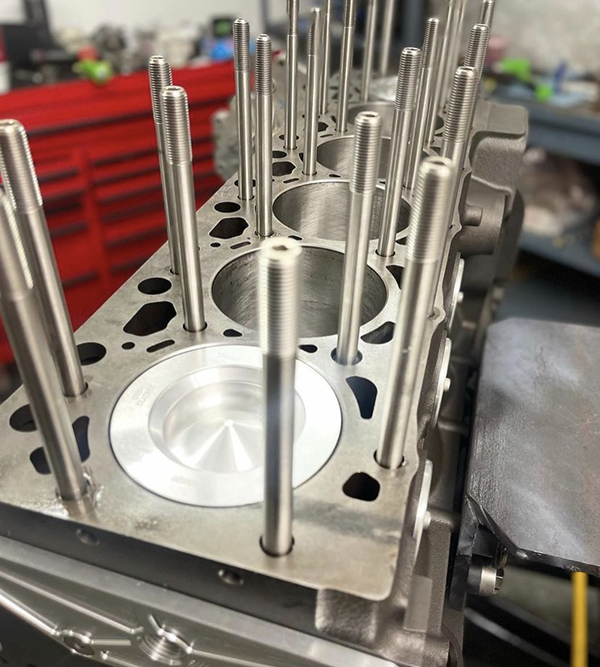
“You have to have the right gasket and the right clamp load and crush on the head gasket. Once you get into extreme performance, that’s when you get into fire ringing the block and different things like that.”
According to Zeigler, not many people mess up when it comes to the head studs themselves, but rather the prep work involved.
“Making sure the deck surface is clean is critical, especially with these multilayer steel gaskets – the surface finish has to be right,” Zeigler says. “You want the surface finish to be uniform the whole way.”
Weighing Your Options
Pretty much all engine components these days have numerous options available to customers. Engine hardware, however, may be one of the few areas where ARP is the clear go-to brand based on quality, experience and offerings. That dominance is still far from being challenged, but more players are entering the space such as Gator Fasteners, and the supply chain issues of late are giving others an advantage.
“Nobody can touch the success ARP has,” Zeigler admits. “However, I think Gator Fasteners could potentially have that success as long as they don’t get out of whack on the price point. The price point is right and the quality is definitely there. I think it’ll be a very good option as opposed to some of the ARP stuff since we’re waiting months on those right now.”
Raschke admitted ARP is being challenged, as are so many manufacturers, with trying to keep up with demand. He says the company is working on getting those wait times reduced and capacity increased.
“It’s hard to beat the stuff ARP gives you, but it seems like Gator Fasteners could be an equal option.” EB